Construction, automotive manufacturing, defense contracting, excavation and manufacturing industries all utilize these often heavy-duty pumps in machines including cranes, lifts and even the engines that run them. While hydraulic piston and gear pumps are predominantly used in industrial contexts to push, pull and lift heavy loads, hydraulic pumps have many other uses. Electric hydraulic pumps can be used as generators, hydraulic water pumps transfer water and hydraulic clutch pumps pressurize fluid for vehicle power steering, among other mechanical operations. Read More…
All World Machinery Supply offers high-quality, affordable pumps, motors, and power units from reputable brands like Daikin, Nachi, Eaton, Tokimec, NOP, Grundfos, Yuken, and Fuji . Our team of representatives and engineers can find or cross any pump/mortor to what you are looking for. We can even help you design a custom application suited to your fit your needs.
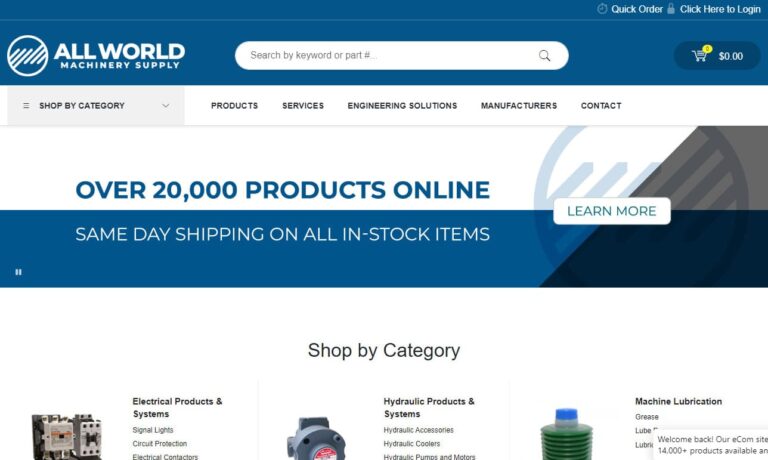
Perfection Hydraulics manufactures, distributes, and services hydraulic cylinders, hydraulic pumps, hydraulic valves, hydraulic gear pumps, and other hydraulic components for heavy equipment. Our products provide you with the best value available for today’s dynamic industry. With our reputation for quality and reliability, you can rely on us for your heavy duty hydraulics needs.
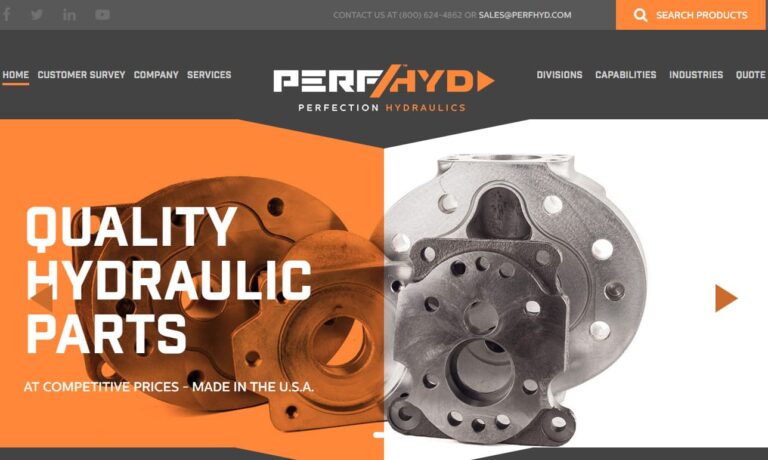
Enerpac is the global leader in high-force tools and equipment used in industrial markets. Our focus is to provide our customers with the most extensive line of products and accessories that maximize force to increase productivity and make work safer and easier to perform. Our comprehensive family of tools and equipment deliver reliable and dependable performance for any industrial segment.
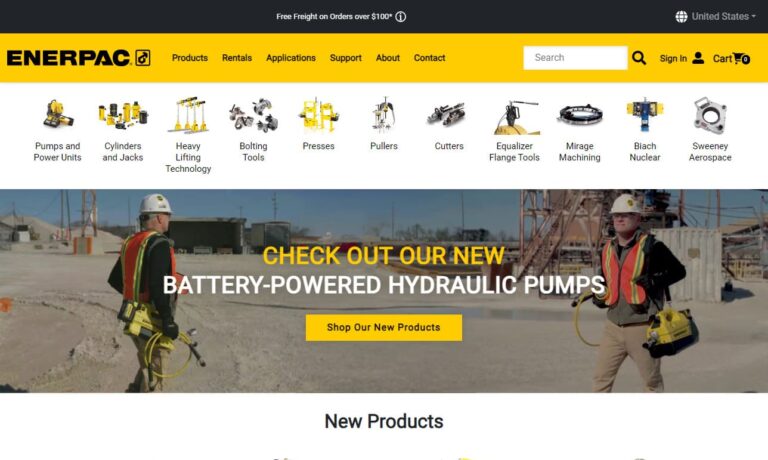
Over 50 years, Hydro Leduc has developed more than 100 patents because of our passion for innovation in the hydraulics field. We find solutions to our customers’ most complex and demanding applications for piston pumps, hydraulic motors, hydro-pneumatic accumulators and custom hydraulic components.
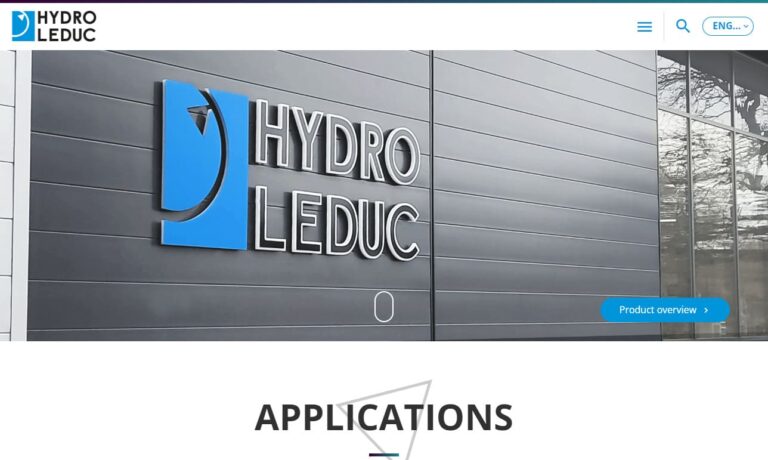
More Hydrolic Pump Manufacturers
As the pumps themselves are as varied as the tasks they help to accomplish, it is important to consider the intended use when selecting a hydraulic pump. Size, weight, operating pressure, power source, maximum pressure and fluid flow and operating speed all vary considerably and are widely available in standard and customized packages. Body material should also be application-specific. Durable metals such as stainless steel, aluminum and iron are popular in hydraulic cylinder construction, though thermoplastics and ceramics such as silicon carbide and alumina are also widely used for their heat and corrosion resistance. The materials must be able to withstand the constant wear of the pumping action and also be compatible with the hydraulic fluids required to operate the system.
As with many cylinder-based systems, hydraulic cylinders can be divided into single and double-action categories. Single-action pumps operate in only one direction, while double-acting systems are multidirectional. Additional divisions can be made based on the mechanism used to pressurize the hydraulic fluids. Pistons or gears are the most popular devices, though vanes within the cylinder can also be utilized to compress liquids and create kinetic energy. Despite these variations, all hydraulic pumps have the same basic components.
A reservoir is needed to house the fluids, which are often oil or water-based composites. Tubes or hoses attached to the reservoir carry the fluids to the hydraulic cylinder, or they can be moved by cylinders that have both an intake check valve and a discharge check valve located at opposite ends. When the pump or gears are drawn back, they create a vacuum that pulls hydraulic fluid from the reservoir into the enclosed cylinder.
When the vacuum is released the intake valve closes, trapping the fluid, which is then compressed by the returning gears or pistons. Pumping of this nature continues until the pressure is great enough to force the liquid through the discharge valve. It is important that all elements of the pump are properly calibrated, as leaks will diminish the vacuum and pressurization capacities of the mechanism. CNC machining and other precision manufacturing processes are therefore used to produce the pump parts.